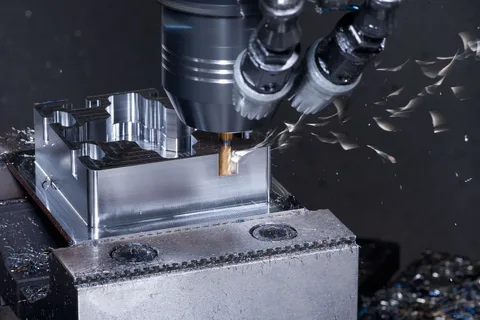
CNC machining is a cornerstone of modern manufacturing, playing a pivotal role in the creation of precision-engineered parts and products across industries such as aerospace, automotive, medical, and electronics. Understanding what CNC machining is and its significance in the manufacturing landscape is crucial for anyone involved in the production of high-quality, complex components. In this article, we will explore the evolution of CNC machining and how it has revolutionized precision engineering, with a particular focus on its development, technological advancements, and its vital role in the future of manufacturing.
The Basics of CNC Machining
CNC machining, or Computer Numerical Control machining, refers to the process of using computers to control machine tools such as lathes, mills, routers, and grinders. In a CNC system, a computer program (often a CAD/CAM file) directs the machine’s movements to create parts with high precision and repeatability. This process replaces the need for manual operation, significantly improving efficiency, accuracy, and the complexity of the parts that can be produced. But what is CNC machining really in practice?
At its core, CNC machining involves the use of pre-programmed software to control the movement of various machinery components along multiple axes. This allows for intricate designs, complex geometries, and extremely fine tolerances to be maintained with minimal human intervention. CNC machines can create parts out of various materials, including metals, plastics, and composites, making them a versatile and invaluable tool in modern manufacturing. The transition from manual machining to CNC machining marked a significant leap forward in the precision engineering industry.
The History and Evolution of CNC Machining
The journey of CNC machining began in the mid-20th century, with early developments rooted in the need for increased precision and automation in manufacturing. Before the advent of CNC machining, traditional machine tools were operated manually by skilled machinists who would perform each step of the process. This was time-consuming and often resulted in inconsistencies and errors in the final product. The need for automation to improve efficiency and reduce human error led to the invention of the CNC machine.
The first CNC machines were introduced in the 1950s and 1960s, with the development of numerical control (NC) systems, which were controlled by punched tape. This was a revolutionary step, allowing machines to execute more complex movements automatically. By the 1970s, the emergence of more sophisticated CNC systems, powered by computers, allowed for greater precision and flexibility. This marked the beginning of the transformation that would lead to the highly automated, computer-controlled machines we rely on today. Over the decades, advancements in software, hardware, and the materials used in CNC machining have led to even more precise and efficient methods of production.
How CNC Machining Works: The Process Breakdown
Understanding the question, “What is CNC machining?” goes beyond the basics of machine tools and software. To grasp how CNC machining works, it’s essential to look at the entire process, from design to finished product. CNC machining starts with the creation of a detailed design, usually through CAD (Computer-Aided Design) software, which outlines the specific dimensions and features of the part to be manufactured. This design is then translated into machine instructions using CAM (Computer-Aided Manufacturing) software, which generates the code that tells the machine exactly how to perform each task.
Once the code is generated, it’s input into the CNC machine, which follows the instructions to cut, drill, mill, or grind the material into the desired shape. CNC machines use various tools, including rotating cutting tools and stationary fixtures, to shape the material precisely. The machine works in multiple axes, with most modern CNC machines operating along three, four, or even five axes. This multidimensional control allows for the creation of complex shapes and geometries that would be difficult, if not impossible, to achieve using traditional manual machining techniques. The process is repeated automatically, with the machine making minor adjustments based on feedback from sensors, ensuring that the part meets the exact specifications.
Advantages of CNC Machining in Precision Engineering
The widespread adoption of CNC machining in precision engineering has brought about numerous advantages, transforming the way complex parts are produced. One of the key benefits of CNC machining is its ability to produce highly accurate and consistent parts. Once a CNC machine is set up and programmed, it can repeat the same task with incredible precision, ensuring that each part is identical to the last. This consistency is crucial in industries like aerospace and medical device manufacturing, where even minute variations can result in significant failures.
Another significant advantage is the increased efficiency of the manufacturing process. CNC machines can operate continuously without the need for breaks, allowing for high-volume production with minimal downtime. Additionally, CNC machining reduces the need for skilled labor, as machines can perform most tasks with minimal human intervention. This shift to automation has also led to faster production cycles, lower labor costs, and the ability to produce more complex designs that would have been difficult or too costly to manufacture manually. The ability to quickly switch between different designs and the minimal setup time for CNC machines makes them incredibly versatile, further solidifying their role in modern precision engineering.
The Future of CNC Machining and Emerging Trends
As technology continues to advance, so too does the field of CNC machining. The future of CNC machining is closely tied to the integration of new technologies, such as artificial intelligence (AI), machine learning, and the Internet of Things (IoT). These technologies are already beginning to influence CNC machining, providing even more precise control over machines and enabling real-time monitoring and adjustments. For instance, AI-powered systems can analyze machine performance data to predict maintenance needs, reducing downtime and improving overall efficiency.
Additive manufacturing, or 3D printing, is another technology that is merging with CNC machining to create hybrid manufacturing processes. While CNC machining is subtractive (removing material to create a part), additive manufacturing builds parts layer by layer. The combination of these two techniques allows for even greater design flexibility, enabling the creation of intricate geometries that were previously impossible. Additionally, advancements in materials science are leading to the development of new materials that can be used in CNC machining, such as composites, superalloys, and advanced polymers. These innovations promise to further expand the capabilities of CNC machining and its role in shaping the future of precision engineering.
Conclusion
CNC machining has come a long way since its inception, revolutionizing the manufacturing industry by enabling the creation of high-precision parts that meet the exact specifications required in industries ranging from aerospace to medical devices. From its humble beginnings to the sophisticated machines of today, CNC machining has continuously evolved, driven by technological advancements in software, hardware, and materials. As we look to the future, CNC machining will undoubtedly continue to play a critical role in shaping the world of precision engineering, driven by emerging technologies and innovations that promise to enhance the capabilities and efficiency of these machines. Whether you’re a seasoned engineer or someone just beginning to explore the world of manufacturing, understanding what CNC machining is and how it works will provide invaluable insight into the heart of modern precision engineering.