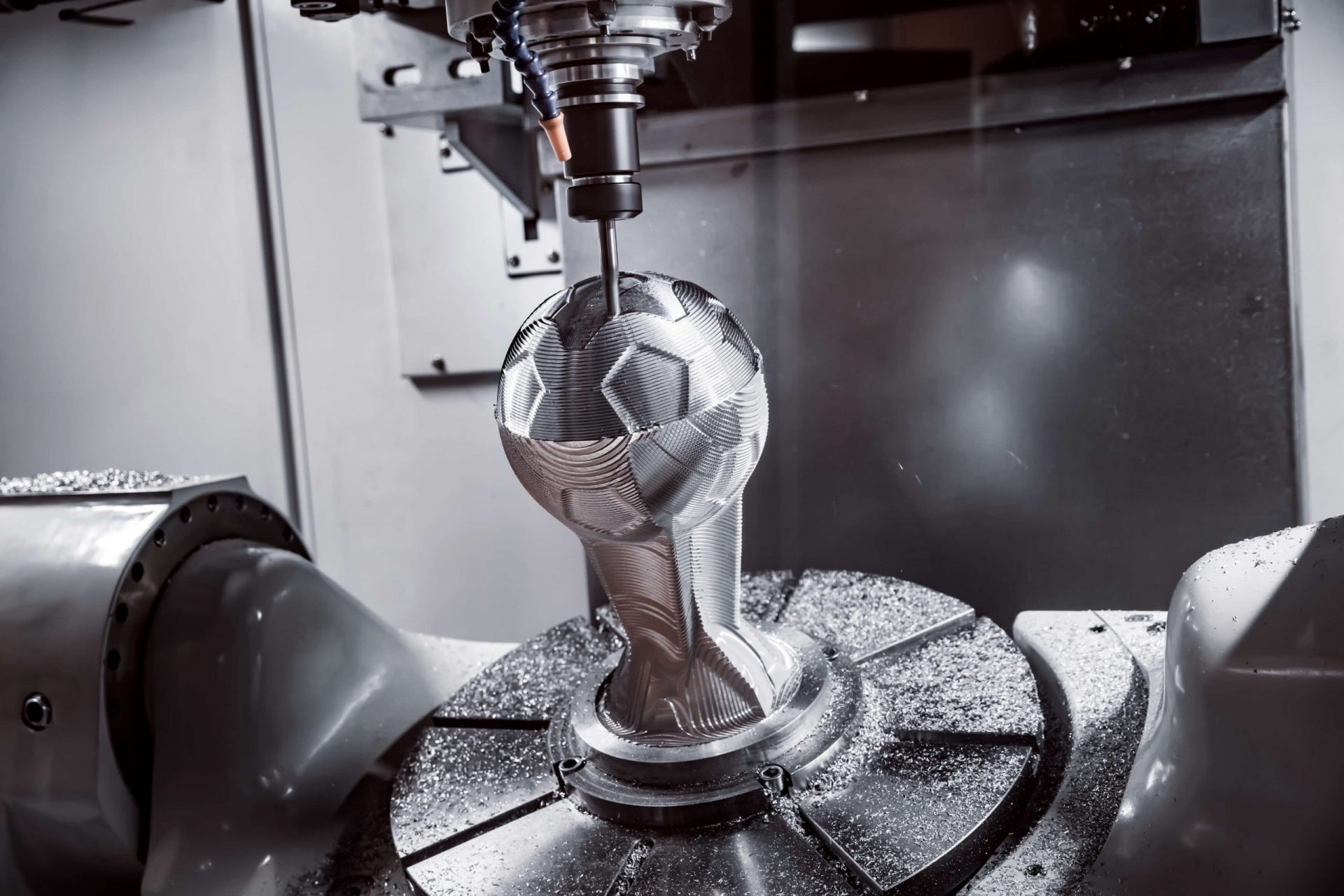
In the rapidly evolving world of manufacturing, precision and efficiency are critical. Over the years, Computer Numerical Control (CNC) machining has emerged as a transformative technology, revolutionizing the way complex parts and components are produced. CNC Machininig utilizes computer programming to control machinery and perform intricate cutting, drilling, milling, and turning operations on a wide range of materials. This method has significantly reduced production times, improved accuracy, and enabled the creation of parts with highly complex geometries. In this article, we will delve into CNC machining, its types, benefits, applications, and the reasons why it’s considered a game-changer for the manufacturing sector.
What is CNC Machining?
CNC machining refers to a manufacturing process where pre-programmed computer software controls the movement and operation of machinery. Unlike traditional manual machining, where operators guide tools, CNC machines are fully automated. This allows for precise control over the operations, including speed, feed rate, and positioning.
The process begins with the creation of a 3D computer-aided design (CAD) model of the part. This design is then converted into a set of instructions (G-code) that guides the machine’s movements. The CNC machine follows these instructions to remove material from a solid block or workpiece, shaping it into the desired final product.
This method of manufacturing has gained immense popularity across industries because of its ability to produce high-precision parts and components efficiently and with minimal human intervention.
Key Types of CNC Machines
CNC machines come in various forms, each designed for different manufacturing purposes. Some of the most common types of CNC machines used today include:
1. CNC Milling Machines
CNC milling machines are one of the most versatile and widely used types of CNC machines. They use rotating cutting tools to remove material from a stationary workpiece. CNC mills are often equipped with multi-axis capabilities, allowing them to create complex shapes and precise features.
Features:
- Multiple Axes: Modern CNC milling machines can operate along three, four, or even five axes, providing the ability to create intricate designs with various orientations.
- Precision: CNC milling ensures that the parts produced are highly accurate and meet tight tolerances.
Applications:
CNC milling is commonly used for producing components like engine parts, housings, molds, and precision tools in industries such as aerospace, automotive, and medical device manufacturing.
2. CNC Lathes
CNC lathes are primarily used for creating cylindrical parts. The workpiece is rotated while a stationary cutting tool is applied to shape the material. CNC lathes are ideal for producing symmetrical parts with high precision.
Features:
- Rotating Workpieces: The workpiece is spun at high speeds, while the tool moves in various directions to remove material and shape the object.
- Efficient Production: CNC lathes allow for high-speed production of round and cylindrical parts with minimal material wastage.
Applications:
Commonly used in automotive, aerospace, and oil and gas industries, CNC lathes are used to make parts such as shafts, piston rods, and bearings.
3. CNC Routers
CNC routers are specialized machines designed for cutting and shaping softer materials like wood, plastics, and foam. These machines are similar to CNC milling machines but are typically used for large-scale cutting and engraving applications.
Features:
- Large Workpieces: CNC routers can accommodate large sheets of material, making them ideal for high-volume production.
- Versatile Cutting: CNC routers can cut, drill, and engrave, offering flexibility for various designs.
Applications:
Commonly used in industries like woodworking, cabinetry, and signage, CNC routers are ideal for creating detailed cuts in materials such as wood, plastics, and acrylics.
4. CNC EDM (Electrical Discharge Machining)
CNC EDM machines use electrical discharges (sparks) to remove material from the workpiece. This method is ideal for creating detailed, intricate designs and is particularly useful for machining hard metals.
Features:
- High Precision: CNC EDM is capable of achieving very fine details and intricate geometries that would be impossible with traditional cutting methods.
- No Physical Contact: Since EDM uses electrical discharges rather than mechanical cutting tools, there is no tool wear.
Applications:
CNC EDM is used in industries such as aerospace, automotive, and mold-making to produce precise components, dies, and molds.
5. CNC Plasma Cutters
CNC plasma cutters use a high-temperature plasma arc to cut through conductive materials, such as metals. Plasma cutting is a fast and efficient process, ideal for thick metals that would be challenging to cut with traditional methods.
Features:
- High-Speed Cutting: CNC plasma cutters offer quick cutting speeds, making them perfect for large-scale production.
- Precision: The accuracy of plasma cutting ensures that the parts produced meet the required specifications.
Applications:
CNC plasma cutters are widely used in the metal fabrication industry, especially for cutting steel, aluminum, and other metals for structural components and industrial applications.
Advantages of CNC Machining
CNC machining provides several distinct advantages, making it a preferred choice in the manufacturing industry. Some of the key benefits include:
1. Enhanced Precision and Accuracy
CNC machines are designed to produce parts with extremely high precision and tight tolerances. The computerized control ensures that each part is created exactly to the specifications, minimizing human error and reducing the likelihood of defects.
2. Increased Efficiency and Speed
Once programmed, CNC machines can operate continuously, working 24/7 with minimal supervision. This significantly reduces production times, especially for high-volume runs, and allows manufacturers to produce large quantities of parts in a short period.
3. Complex Geometries and Customization
CNC machining allows manufacturers to produce complex, detailed, and intricate designs that would be difficult or impossible to achieve with traditional methods. The flexibility of CNC machines enables manufacturers to quickly modify designs and create customized components based on specific customer requirements.
4. Lower Labor Costs
Although CNC machines require skilled operators to set up and program, they significantly reduce the need for manual labor. The automation provided by CNC machines allows manufacturers to produce parts with less human involvement, reducing labor costs over time.
5. Consistency and Reproducibility
Since CNC machines operate based on pre-programmed instructions, they can replicate the same part with high consistency and repeatability. This makes CNC machining an ideal solution for industries where high volumes of identical parts are required, such as automotive and consumer electronics.
6. Improved Safety
CNC machining reduces the need for human operators to interact directly with machinery during the cutting process. With automation in place, the risk of operator injuries or accidents is greatly minimized, creating a safer work environment.
CNC Machining Applications Across Industries
CNC machining plays a vital role in several industries. The ability to produce precision parts quickly and efficiently makes it invaluable across a wide range of applications.
1. Aerospace and Defense
The aerospace industry demands high-precision components that meet rigorous standards for safety and performance. CNC machining is used extensively in the production of aircraft parts, engine components, and defense systems. These parts require precise tolerances, and CNC machining ensures that each component fits within the required specifications.
2. Automotive Industry
The automotive industry relies on CNC machining for the production of critical components such as engine blocks, transmission parts, and chassis. CNC machining’s ability to produce complex shapes with high accuracy makes it ideal for automotive manufacturing, particularly for creating prototypes and low-volume production runs.
3. Medical Devices
In the medical field, CNC machining is essential for the production of custom implants, surgical instruments, and diagnostic equipment. The technology’s precision ensures that medical devices meet strict standards for quality and safety. CNC machining also allows for the production of patient-specific components, such as customized prosthetics and implants.
4. Consumer Electronics
CNC machining is used to create parts for a wide range of consumer electronics, including smartphones, computers, and televisions. The ability to create intricate components with tight tolerances ensures that electronic devices are functional, durable, and meet the required standards.
5. Tooling and Molds
Many industries rely on CNC machining to produce molds and tooling for various manufacturing processes, such as injection molding, die casting, and stamping. CNC machines can create highly accurate molds with complex geometries, ensuring high-quality production of end products.
Conclusion
CNC machining has transformed the manufacturing industry by enabling manufacturers to produce high-quality, precise parts quickly and cost-effectively. With its ability to create complex geometries, reduce production times, and enhance efficiency, CNC machining has become indispensable in industries ranging from aerospace and automotive to medical devices and consumer electronics.
As CNC technology continues to advance, it is expected to drive further innovation, improve manufacturing processes, and enhance production capabilities. Whether for low-volume production or mass manufacturing, CNC machining will continue to play a critical role in shaping the future of modern manufacturing.