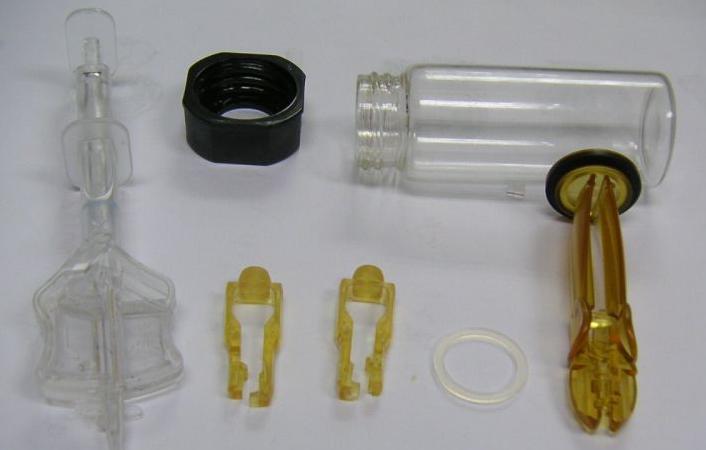
The Complete Guide to Injection Molding Manufacturing
As an industry veteran with over two decades of experience, I’ve witnessed the remarkable evolution of injection molding manufacturing practices in China and globally. Today’s plastic manufacturing landscape has transformed dramatically, incorporating advanced technologies and innovative approaches that were unimaginable when I first started.
Understanding Modern Injection Molding Technology
The injection molding process has become increasingly sophisticated over the years. Modern machines now incorporate artificial intelligence and machine learning capabilities, enabling unprecedented levels of precision and efficiency. These technological advancements have revolutionized how we approach custom plastic component manufacturing and design optimization.
Key Components of an Injection Molding System
- Injection Unit: The heart of the system, incorporating advanced servo-driven mechanisms that ensure precise material delivery and consistent shot sizes across production runs.
- Clamping Unit: Modern hydraulic or electric clamping systems that provide the necessary force to keep molds closed during injection, featuring sophisticated pressure monitoring systems.
- Control System: State-of-the-art PLC controllers with intuitive interfaces that allow for real-time process monitoring and adjustments.
Material Selection and Optimization
The choice of materials significantly impacts product quality and cost-effectiveness. Here’s what you need to consider:
- Material Properties
- Mechanical strength and durability requirements
- Temperature resistance and thermal stability
- Chemical resistance and environmental considerations
- Processing Parameters
- Melt flow characteristics
- Cooling time requirements
- Shrinkage and warpage control
Common Materials in Modern Injection Molding
Material Type | Applications | Key Properties |
---|---|---|
Thermoplastics | Consumer goods, automotive parts | Recyclable, versatile |
Engineering Plastics | Industrial components | High strength, heat resistant |
Bio-based Plastics | Sustainable packaging | Eco-friendly, biodegradable |
Design Considerations for Optimal Results
Creating effective injection-molded parts requires careful attention to design principles. Here are critical factors to consider:
- Wall Thickness Consistency: Maintain uniform wall thickness whenever possible to prevent warping and ensure proper filling. Variations should not exceed 10% of the nominal thickness.
- Draft Angles: Include appropriate draft angles, typically between 1° and 5°, to facilitate easy part removal from the mold.
- Gate Location: Strategic placement of gates affects flow patterns and weld line formation, ultimately impacting part quality and appearance.
Advanced Design Features
The evolution of design capabilities has introduced several innovative features:
- Living Hinges
- Allows for integrated hinge designs
- Reduces assembly costs
- Improves product functionality
- Snap Fits
- Enables tool-free assembly
- Reduces manufacturing complexity
- Enhances product serviceability