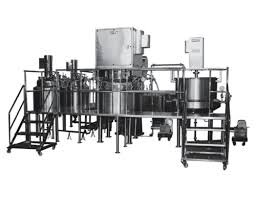
Introduction
Good Manufacturing Practices (GMP) compliance is a crucial aspect of ointment manufacturing, ensuring that products meet quality, safety, and efficacy standards. Regulatory bodies such as the FDA (U.S. Food and Drug Administration) and WHO (World Health Organization) set GMP guidelines to prevent contamination, ensure consistency, and protect consumers. This article explores the importance of GMP compliance in ointment manufacturing and the key requirements for maintaining a GMP-certified facility.
Importance of GMP in Ointment Manufacturing
GMP compliance is essential in the pharmaceutical and cosmetic industries, where ointments are widely used for medicinal and skincare purposes. The primary reasons for adhering to GMP standards include:
- Consumer Safety: GMP guidelines ensure that ointments are free from harmful contaminants and are safe for application.
- Product Consistency: Adhering to GMP protocols ensures that each batch of ointment Plant meets the same quality standards.
- Regulatory Compliance: Manufacturers must comply with national and international regulations to avoid legal issues and maintain their market position.
- Market Credibility: A GMP certification enhances consumer trust and increases business opportunities by ensuring high product standards.
Key GMP Requirements for Ointment Manufacturing
To achieve GMP compliance, manufacturers must follow stringent guidelines covering various aspects of production. Some of the essential GMP requirements include:
1. Facility and Equipment Standards
- Manufacturing facilities must be designed to prevent contamination and cross-contamination.
- Equipment should be well-maintained, regularly calibrated, and cleaned according to documented procedures.
- Adequate ventilation, temperature control, and humidity management are necessary to ensure product stability.
2. Raw Material Quality Control
- All raw materials, including active pharmaceutical ingredients (APIs) and excipients, must be sourced from reliable suppliers.
- Quality testing should be conducted to verify purity, potency, and compliance with predefined specifications.
- Materials should be stored in designated areas under controlled conditions to prevent degradation.
3. Manufacturing Process Control
- The manufacturing process must be clearly defined, validated, and documented to ensure repeatability and consistency.
- Operators should follow Standard Operating Procedures (SOPs) to maintain process integrity.
- Critical process parameters, such as mixing time and temperature, should be monitored and recorded.
4. Personnel Training and Hygiene
- Employees must be adequately trained in GMP requirements, hygiene, and safety protocols.
- Staff should wear appropriate protective clothing, gloves, and masks to prevent contamination.
- Regular health checks should be conducted to ensure personnel do not pose a risk to product integrity.
5. Quality Assurance and Testing
- Finished products must undergo rigorous testing, including microbial analysis, viscosity tests, and stability studies.
- In-process quality checks should be performed at different production stages to detect deviations early.
- A robust quality management system should be in place to document all test results and corrective actions.
6. Documentation and Record-Keeping
- Every stage of production must be documented in a structured manner to ensure traceability and accountability.
- Batch manufacturing records should be maintained, detailing raw material usage, process conditions, and test results.
- Any deviations, errors, or non-conformities should be recorded, investigated, and rectified promptly.
7. Packaging and Labeling Compliance
- Ointments should be packaged in materials that prevent contamination and preserve stability.
- Labels must include essential information such as ingredients, expiration dates, and usage instructions.
- Tamper-evident packaging should be used to ensure product integrity.
8. Storage and Distribution Controls
- Storage conditions should be maintained as per product specifications to prevent degradation.
- Distribution processes should ensure that ointments reach consumers without compromising quality.
- A tracking system should be in place to recall defective batches if necessary.
Common Challenges in GMP Compliance
While GMP compliance is crucial, manufacturers often face challenges such as:
- High Implementation Costs: Setting up a GMP-compliant facility requires significant investment in infrastructure, equipment, and training.
- Regulatory Updates: Keeping up with changing regulations and standards can be demanding.
- Maintaining Documentation: Extensive documentation is necessary, which requires meticulous record-keeping and audits.
- Ensuring Consistency: Variability in raw materials and human errors can impact product consistency.
Best Practices for Achieving GMP Compliance
To overcome challenges and maintain GMP compliance, manufacturers should:
- Invest in Staff Training: Regular training sessions ensure that employees are updated on GMP protocols.
- Conduct Internal Audits: Routine audits help identify potential compliance gaps and areas for improvement.
- Implement a Digital Quality Management System (QMS): Automated documentation and tracking systems enhance efficiency and accuracy.
- Engage with Regulatory Experts: Consulting with regulatory specialists can help navigate complex compliance requirements.
Conclusion
GMP compliance is essential for ensuring the safety, efficacy, and quality of ointments. By adhering to GMP guidelines, manufacturers can prevent contamination, ensure product consistency, and meet regulatory requirements. Although maintaining compliance can be challenging, implementing best practices, investing in training, and utilizing modern quality management tools can help manufacturers achieve and sustain GMP certification. Ensuring GMP compliance not only protects consumers but also enhances a company’s reputation and market success.