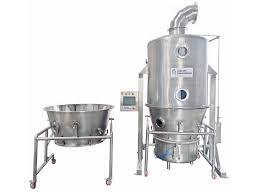
Introduction
In various industries, efficient drying techniques play a crucial role in ensuring the quality, stability, and usability of different products. One such advanced drying technology is the Fluid Bed Dryer (FBD), which has transformed the way materials are dried, making the process faster and more uniform. This guide will provide a comprehensive understanding of fluid bed dryers, their working principles, benefits, applications, and how they contribute to efficiency in industrial drying processes.
What is a Fluid Bed Dryer?
A Fluid Bed Dryer (FBD) is a drying equipment that uses the principle of fluidization to dry granular, powdered, or crystalline materials efficiently. In this process, hot air is passed through a perforated bed containing the material, causing it to behave like a fluid. This ensures uniform heat distribution and faster drying compared to traditional drying methods.
How Does a Fluid Bed Dryer Work?
The working mechanism of a fluid bed dryer involves several key steps:
-
Loading the Material: The wet material is placed inside the drying chamber, usually in a perforated container or bowl.
-
Fluidization Process: Heated air is introduced from below the perforated bed, causing the particles to lift and move freely.
-
Heat Transfer and Moisture Evaporation: The continuous movement of particles ensures even heat transfer, leading to uniform moisture evaporation.
-
Exhaust and Filtration: The moist air is filtered and exhausted, while dry material remains in the chamber.
-
Discharge of Dried Material: Once the desired moisture level is achieved, the dried product is removed for further processing or packaging.
Types of Fluid Bed Dryers
Fluid bed dryers come in various types, each suited for specific applications:
-
Batch Fluid Bed Dryer: Used for small-scale production where drying occurs in controlled batches.
-
Continuous Fluid Bed Dryer: Ideal for large-scale industrial drying, where material moves continuously through the drying zone.
-
Vibratory Fluid Bed Dryer: Utilizes vibration along with airflow to enhance drying efficiency for materials with irregular shapes.
-
Rotary Fluid Bed Dryer: Features rotating mechanisms to prevent material clumping and improve drying uniformity.
Advantages of Using a Fluid Bed Dryer
Fluid bed dryers offer several benefits over traditional drying techniques, making them a preferred choice in various industries:
-
Faster Drying Time: The fluidization process enhances heat and mass transfer, reducing drying time significantly.
-
Uniform Drying: Even heat distribution ensures consistent drying, minimizing the risk of over-drying or under-drying.
-
Energy Efficiency: Lower energy consumption compared to conventional dryers, making it a cost-effective solution.
-
Improved Product Quality: Prevents material degradation, maintaining the integrity of heat-sensitive substances.
-
Flexibility: Suitable for drying a wide range of materials, including powders, granules, and crystals.
-
Scalability: Available in different sizes and configurations to meet industrial requirements.
-
Easy Cleaning and Maintenance: Simple design allows for quick cleaning and minimal downtime.
Industrial Applications of Fluid Bed Dryers
Fluid bed dryers are widely used across various industries due to their versatility and efficiency. Some key applications include:
-
Pharmaceutical Industry: Used for drying granules, powders, and tablet coatings while maintaining their properties.
-
Food Industry: Essential for drying food products such as spices, coffee, and dairy powders without compromising nutritional value.
-
Chemical Industry: Helps in drying chemical powders and granules, improving product consistency and stability.
-
Agricultural Sector: Utilized for drying seeds, fertilizers, and pesticides to enhance storage life and usability.
-
Cosmetic Industry: Plays a crucial role in drying powders used in cosmetics and personal care products.
-
Mineral Processing: Assists in drying minerals, ores, and other geological materials efficiently.
Factors to Consider When Choosing a Fluid Bed Dryer
Selecting the right fluid bed dryer depends on several factors, ensuring optimal performance and efficiency:
-
Material Characteristics: Consider particle size, moisture content, and heat sensitivity before choosing a dryer.
-
Production Capacity: Assess batch or continuous processing needs to match industry requirements.
-
Energy Consumption: Opt for energy-efficient models to minimize operational costs.
-
Space and Installation Requirements: Ensure compatibility with existing production lines and available space.
-
Automation and Control Features: Look for advanced controls to regulate drying parameters precisely.
-
Cleaning and Maintenance Needs: Choose a design that allows for easy cleaning, reducing downtime.
Best Practices for Efficient Drying with Fluid Bed Dryers
To maximize efficiency and achieve the best drying results, follow these best practices:
-
Optimize Airflow and Temperature: Adjust settings based on material properties to prevent overheating or inefficient drying.
-
Regular Maintenance: Keep the equipment clean and inspect filters, fans, and nozzles regularly.
-
Monitor Moisture Content: Use sensors to ensure consistent product quality and avoid excessive drying.
-
Proper Loading Techniques: Avoid overloading or underloading the dryer to maintain uniform fluidization.
-
Utilize Advanced Control Systems: Invest in automated systems to optimize drying parameters and enhance process efficiency.
Conclusion
A Fluid Bed Dryer is a powerful tool for achieving efficient and uniform drying across various industries. Its ability to reduce drying time, improve product quality, and enhance energy efficiency makes it a preferred choice for manufacturers. By understanding the working principles, benefits, and applications of fluid bed dryers, industries can optimize their drying processes and improve overall productivity. Whether in pharmaceuticals, food processing, or chemicals, the right fluid bed dryer can significantly impact the quality and consistency of the final product. Investing in the right model, following best practices, and maintaining the equipment properly will ensure maximum efficiency and long-term success.