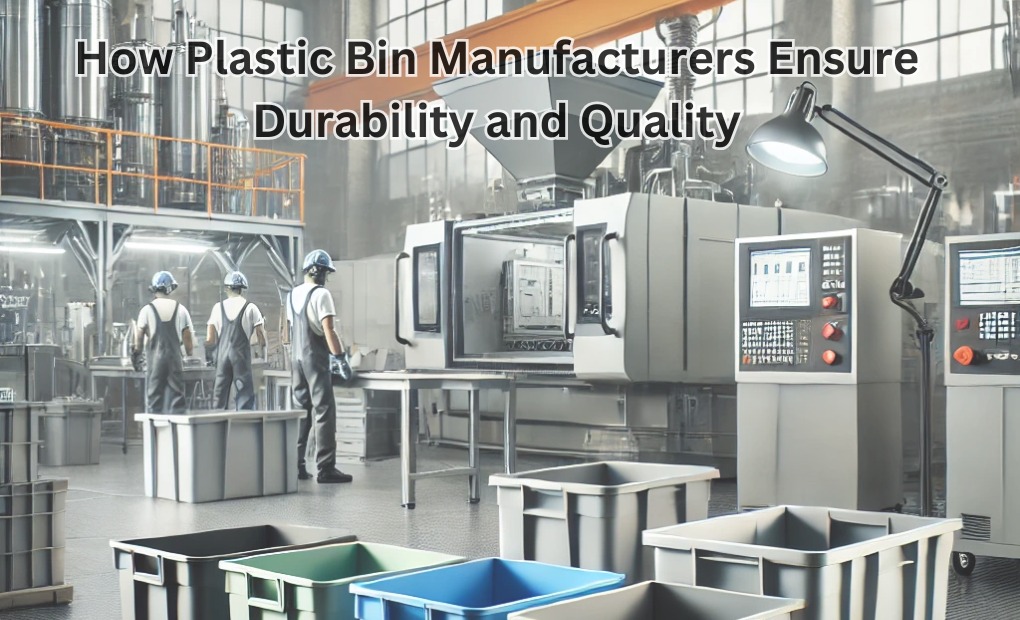
Plastic bins have become an essential part of modern storage, waste management, and industrial applications. Whether used in households, commercial spaces, or industries, the durability and quality of plastic bins play a crucial role in their functionality and longevity. Manufacturers adopt various processes, materials, and quality control measures to ensure that plastic bins meet high standards.
1. Selecting the Right Raw Materials
The durability of plastic bins largely depends on the type of plastic used in manufacturing. High-density polyethylene (HDPE) and polypropylene (PP) are commonly used materials because of their strength, flexibility, and resistance to impact. These plastics offer the following benefits:
-
HDPE (High-Density Polyethylene): Known for its toughness and resistance to chemicals, HDPE is ideal for bins that need to withstand heavy loads and outdoor conditions.
-
Polypropylene (PP): This material provides excellent resistance to wear and tear, making it suitable for storage bins that require frequent handling.
-
Recycled Plastics: Many manufacturers are incorporating recycled plastics to reduce environmental impact while maintaining durability.
2. Advanced Manufacturing Processes
Plastic bin manufacturers use different manufacturing techniques to ensure high-quality products. Some of the most commonly used methods include:
A. Injection Molding
Injection molding is a widely used process that ensures uniform thickness, strength, and durability. The process involves melting plastic resin and injecting it into a mold to create a sturdy and well-shaped bin. Injection-molded bins are highly durable and resistant to cracks and breakage.
B. Blow Molding
Blow molding is another technique used to create hollow plastic bins, especially those designed for large waste disposal. This method enhances impact resistance and allows manufacturers to produce lightweight yet strong bins.
C. Rotational Molding
Rotational molding involves heating and rotating plastic resin within a mold to create seamless and impact-resistant bins. This process is commonly used for large industrial bins that require extra strength.
3. Quality Testing for Durability
Ensuring the durability of plastic bins requires rigorous testing at different stages of production. Some key quality tests include:
A. Load-Bearing Tests
Manufacturers test the weight capacity of bins by applying heavy loads to ensure they can handle the required storage or waste management needs.
B. Impact Resistance Tests
Bins are subjected to controlled drops and impacts to determine their ability to withstand rough handling. This ensures they do not crack or break easily.
C. UV and Weather Resistance Tests
Outdoor plastic bins need to withstand harsh sunlight, rain, and temperature changes. UV resistance tests check how well bins can endure prolonged sun exposure without degrading or becoming brittle.
D. Chemical Resistance Tests
Industrial and medical waste bins must resist exposure to chemicals. Testing ensures that the plastic does not degrade when in contact with acids, solvents, or cleaning agents.
4. Design Features That Improve Durability
Manufacturers incorporate specific design elements to enhance the strength and longevity of plastic bins:
-
Reinforced Walls and Bases: Thickened walls and reinforced bases prevent cracking under pressure.
-
Smooth Interiors: A smooth inner surface prevents dirt buildup, making the bins easier to clean and maintain.
-
Ergonomic Handles and Rims: Properly designed handles make lifting and carrying easier while reducing stress on the bin structure.
-
Ventilation and Drainage Features: Some bins include drainage holes or ventilation slots to prevent moisture buildup and improve hygiene.
5. Sustainable and Eco-Friendly Manufacturing
As environmental concerns grow, many manufacturers are focusing on producing eco-friendly plastic bins. Plastic Bin Manufacturers In Chennai and other industrial hubs are adopting sustainable practices, such as:
-
Using Recycled Plastics: Many bins are now made with a mix of virgin and recycled plastic to reduce environmental impact.
-
Reducing Waste During Production: Manufacturers optimize raw material usage to minimize waste.
-
Developing Biodegradable Options: Research is ongoing into bio-based plastics that decompose naturally over time.
6. Compliance with Industry Standards
Manufacturers must adhere to national and international quality standards to ensure the reliability of plastic bins. Some key certifications include:
-
ISO Certifications: Quality management systems ensure consistent manufacturing processes.
-
RoHS Compliance: Ensures that plastic bins are free from hazardous substances.
-
FDA Approval: Required for bins used in food storage to ensure they are safe for contact with consumables.
Conclusion
The durability and quality of plastic bins depend on the careful selection of materials, advanced manufacturing processes, rigorous testing, and adherence to industry standards. Plastic Bin Manufacturers In Chennai and other major production centers ensure that their products meet the highest quality requirements to serve various industries efficiently. As technology and sustainability initiatives continue to evolve, plastic bins will become even more durable, versatile, and environmentally friendly.