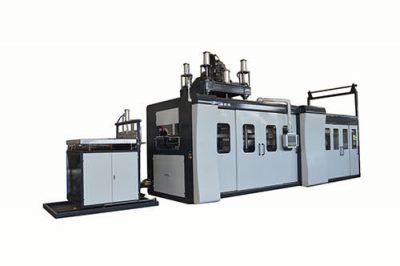
Staying ahead in the quickly changing production scene of today requires embracing cutting-edge technologies that blend accuracy, efficiency, and adaptability. One such innovation that has dramatically transformed the plastic forming industry is the Pressure Thermoforming Machine. Although this technique may not always receive the same spotlight as its counterparts, its ability to produce high-quality, detailed, and cost-effective molded products places it squarely at the center of modern manufacturing.
Whether you’re in the food packaging industry, automotive sector, medical equipment production, or consumer electronics, the need for consistent, durable, and finely detailed plastic components is undeniable. That’s where pressure thermoforming technology stands out—offering an unmatched blend of performance and value.
Understanding Pressure Thermoforming Machines
What Is Pressure Thermoforming?
A heated thermoplastic sheet is pressed into a mold using high-pressure air, frequently at 100 psi or higher, in the specialized plastic molding process known as pressure thermoforming. Unlike traditional vacuum forming, which relies solely on suction, pressure thermoforming machines apply added force to ensure that the plastic conforms precisely to even the most intricate mold details.
This results in sharper edges, finer textures, and improved material distribution, all of which are essential for industries that demand high-performance components.
Components of a Pressure Thermoforming Machine
To fully appreciate the capabilities of this equipment, it’s helpful to understand its key components:
-
- Heating Unit: Prepares the thermoplastic sheet for forming by bringing it to the optimal pliable temperature.
- Forming Station: Houses the mold and uses high-pressure air to shape the sheet.
- Clamping System: keeps the sheet in place during the operation to avoid warping or slipping.
- Cooling System: Rapidly cools the molded product to solidify its shape.
- Control Panel: Controls time, pressure, and temperature to produce reliable outcomes.
The Shanghai Zhanshi Advantage: Next-Gen Pressure Thermoforming Technology
Shanghai Zhanshi Mechanical Equipment Co., Ltd. is a trustworthy manufacturer to choose, standing out for their precision engineering, durability, and commitment to innovation. By integrating advanced automation, user-friendly controls, and robust construction, their Pressure Thermoforming Machines empower businesses to scale production while maintaining exceptional quality.
Whether you’re working with PVC, PET, PS, ABS, or PP sheets, Shanghai Zhanshi Mechanical Equipment Co., Ltd. are designed for optimal material utilization and minimal waste—enhancing both sustainability and profitability.
Why Choose Pressure Thermoforming Over Other Methods?
While several forming techniques exist—such as vacuum forming, injection molding, and twin-sheet forming—pressure thermoforming offers distinct advantages:
1. Higher Detail and Precision
Thanks to the added air pressure, this method captures intricate mold details far better than vacuum forming alone.
2. Cost-Effective Tooling
Compared to injection molding, pressure thermoforming uses less expensive molds—often made from aluminum instead of steel—without compromising detail.
3. Faster Turnaround Times
With quicker mold changes and simpler setup, manufacturers can shift between product lines with ease, ideal for short and medium production runs.
4. Improved Material Distribution
This process provides more uniform wall thickness, resulting in stronger and more aesthetically pleasing parts.
5. Eco-Friendly Production
Thermoforming generates less scrap and consumes less energy compared to injection molding, aligning with growing environmental regulations and standards.
Applications of Pressure Thermoforming Machines
Numerous industries can make use of pressure thermoforming machines because of their versatility. Let’s explore a few notable sectors:
1. Food Packaging
From disposable trays to durable clamshells, thermoformed plastics keep food fresh and protected while offering branding opportunities.
2. Medical Devices
Sterile trays, diagnostic casings, and instrument housings benefit from the precision and hygiene-friendly materials used in pressure thermoforming.
3. Automotive Components
Interior panels, dashboard elements, and trunk liners can be efficiently produced with high detail and durability.
4. Consumer Goods
From appliance housings to electronic device casings, this process delivers sleek designs with functional resilience.
5. Retail and POP Displays
In retail settings, customized thermoformed displays and packaging enhance customer interaction and product visibility.
Customization and Automation: Hallmarks of Zhanshi Equipment
What sets Shanghai Zhanshi Mechanical Equipment Co., Ltd. apart is not just their technical expertise but their commitment to customer-specific customization. Their engineers work closely with clients to tailor machines according to production requirements, including:
-
-
- Sheet size and thickness ranges
- Forming depth
- Mold types and materials
- Cycle speed optimization
- Energy-saving configurations
-
Moreover, Zhanshi’s machines integrate seamlessly with automated feeding systems, trimming units, and stacking devices—maximizing efficiency and reducing labor costs.
Maintenance and Longevity
Investing in a Pressure Thermoforming Machine from Shanghai Zhanshi isn’t just about short-term gains. These machines are built for longevity, with:
-
-
- Corrosion-resistant components
- Easy-access panels for servicing
- Comprehensive technical support
- Optional training for operators and maintenance staff
-
Regular maintenance checks and proper calibration ensure your machine delivers consistent results for years to come.
Future Trends in Pressure Thermoforming
As industries push for smarter and greener solutions, pressure thermoforming is evolving rapidly. Some emerging trends include:
1. IoT-Enabled Monitoring
Manufacturers can identify inefficiencies and avoid downtime with the use of real-time data.
2. Sustainable Materials
There’s growing adoption of biodegradable and recycled thermoplastics, which work seamlessly with Zhanshi’s machines.
3. Hybrid Forming Techniques
combining vacuum and pressure forming to improve form integrity and material distribution even further.
4. 3D Mold Printing
Speeds up mold prototyping and testing phases with additive manufacturing.
In a world where product differentiation and production speed can make or break a brand, leveraging the capabilities of a Pressure Thermoforming Machine is a strategic move. Whether you’re scaling up operations or refining product quality, the technology offers a path to cost-effective, high-performance results across a broad spectrum of applications.
Furthermore, when selecting the ideal companion for this adventure, Shanghai Zhanshi Mechanical Equipment Co., Ltd. delivers not only world-class machinery but also the technical insight, customization, and support to keep your production line ahead of the curve.
FAQs About Pressure Thermoforming Machines
1. What is the difference between vacuum and pressure thermoforming?
Vacuum forming uses suction to pull the heated plastic onto the mold, while pressure thermoforming adds high-pressure air for greater detail and strength.
2. Can pressure thermoforming handle biodegradable materials?
Yes! Many modern Pressure Thermoforming Machines, like those from Zhanshi, are compatible with eco-friendly materials like PLA and recycled PET.
3. How long does it take to set up a pressure thermoforming machine?
Setup times vary depending on machine size and complexity, but Zhanshi’s modular systems and touchscreen interfaces streamline the process significantly.
4. Is pressure thermoforming suitable for mass production?
Absolutely. While ideal for medium-volume runs, automation and efficient cycling make it viable for high-volume applications as well.
5. What industries benefit most from pressure thermoforming?
Food packaging, automotive, medical devices, consumer electronics, and retail display manufacturing all see significant benefits from this forming method.