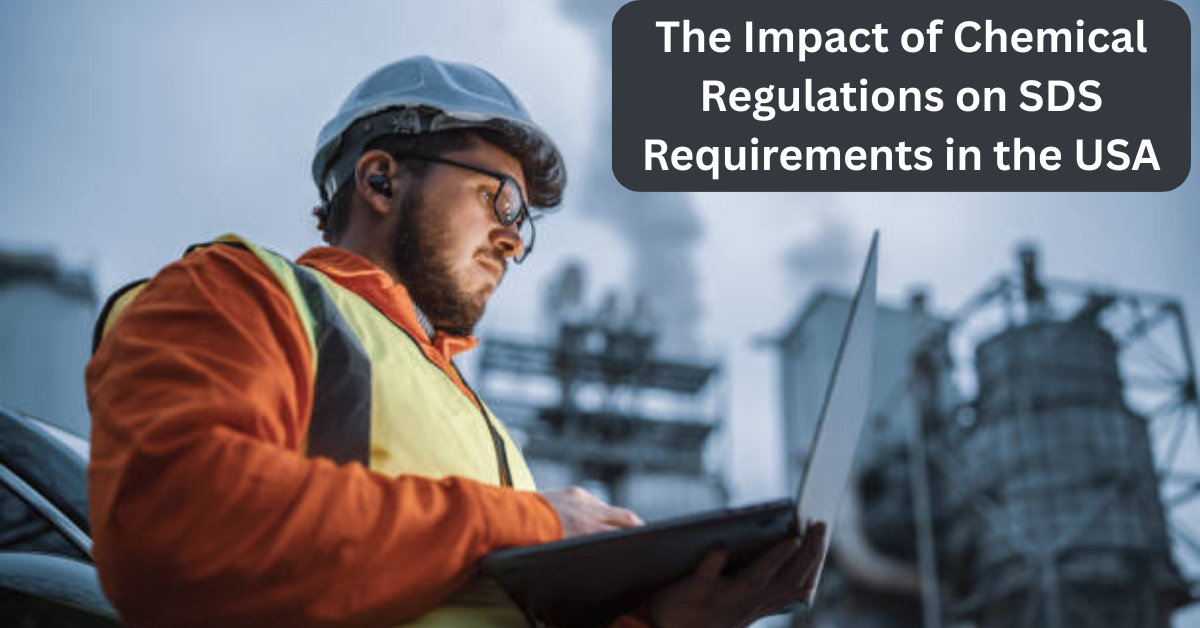
Introduction
Chemical safety is a critical concern for businesses and industries handling hazardous substances. In the USA, Safety Data Sheets (SDS) play a fundamental role in ensuring compliance with chemical regulations and protecting workers, consumers, and the environment. The evolving regulatory landscape affects how companies manage and maintain SDS records. Understanding these changes is crucial for businesses to remain compliant and avoid potential penalties.
For organizations handling hazardous materials, SDS Services play a crucial role in managing compliance, ensuring proper documentation, and keeping up with changing laws. The complexity of chemical regulations makes it essential for businesses to stay informed and implement best practices for SDS management. This article explores how chemical regulations impact SDS requirements, focusing on updates, compliance challenges, and best practices for maintaining compliance in an ever-evolving regulatory environment.
Understanding Safety Data Sheets (SDS)
An SDS (Safety Data Sheet) is a document that provides critical information about a chemical substance, including its composition, hazards, safe handling procedures, emergency measures, and disposal methods. These sheets are essential for ensuring safety in workplaces and maintaining compliance with national and international regulations.
Importance of SDS in Workplace Safety
- Helps workers understand potential hazards and safety precautions.
- Ensures proper chemical labeling and classification.
- Supports emergency responders with necessary first-aid and spill-control measures.
- Aids businesses in meeting Occupational Safety and Health Administration (OSHA) standards.
With regulatory updates, SDS requirements are constantly evolving to enhance workplace safety and environmental responsibility. SDS Services help businesses manage these updates efficiently.
Key Chemical Regulations Affecting SDS Requirements in the USA
Several federal and state regulations dictate SDS compliance in the USA. Below are the most influential chemical safety regulations and their impact on SDS management.
1. OSHA’s Hazard Communication Standard (HCS) and GHS Compliance
The Occupational Safety and Health Administration (OSHA) enforces Hazard Communication Standard (HCS 2012), which aligns with the Globally Harmonized System of Classification and Labeling of Chemicals (GHS).
Impact on SDS Requirements
- Mandatory 16-section format following GHS guidelines.
- Classification of chemical hazards based on physical, health, and environmental risks.
- Standardized pictograms, signal words, hazard statements, and precautionary statements.
- Mandatory periodic updates to reflect regulatory changes or new hazard information.
OSHA periodically updates HCS to incorporate the latest GHS revisions, meaning businesses must frequently review and update their SDS records. Partnering with professional SDS Services ensures timely compliance.
2. EPA’s Toxic Substances Control Act (TSCA)
The Environmental Protection Agency (EPA) oversees the Toxic Substances Control Act (TSCA), which regulates the manufacturing, processing, distribution, and disposal of chemicals.
Impact on SDS Requirements
- New chemical reporting requirements impact SDS updates.
- Businesses must ensure listed substances meet EPA’s risk assessment criteria.
- Companies handling new or restricted chemicals must update SDS to align with TSCA regulations.
- Increased transparency regarding chemical exposure risks and environmental impact.
3. The Emergency Planning and Community Right-to-Know Act (EPCRA)
EPCRA is designed to improve community safety by requiring businesses to report hazardous substances stored or used in their facilities.
Impact on SDS Requirements
- Facilities must submit SDS for hazardous chemicals to local emergency planning authorities.
- Compliance with Tier II chemical inventory reporting requirements.
- Ensures communities have access to chemical safety information to prepare for potential hazards.
4. State-Specific Chemical Regulations
Several states impose additional regulations that affect SDS management, particularly California’s Proposition 65, which mandates labeling and disclosure of chemicals known to cause health risks.
Impact on SDS Requirements
- Businesses selling products in certain states must update SDS to reflect state-specific disclosure requirements.
- Additional warnings and hazard information may be required for listed substances.
- Companies operating in multiple states must ensure compliance with varied local regulations.
Challenges in SDS Compliance for Businesses
1. Keeping Up with Regulatory Changes
Regulations governing chemical safety are frequently updated, making it challenging for businesses to maintain up-to-date SDS records.
2. Managing SDS for Large Inventories
Organizations dealing with hundreds or thousands of chemicals may struggle to ensure all SDS records are correctly managed and easily accessible.
3. Ensuring Accurate SDS Translation and Global Compliance
Businesses operating internationally must ensure SDS comply with varied regional regulations and languages, which requires professional SDS Services.
4. Digital SDS Management and Data Security
While many companies are transitioning to digital SDS management systems, ensuring data security and easy access to employees remains a key challenge.
5. Training and Employee Awareness
- Businesses must ensure employees understand how to read and apply SDS information.
- Regular training sessions can help workers stay updated with changing safety protocols.
- Lack of proper SDS usage knowledge can result in workplace accidents and regulatory non-compliance.
Best Practices for SDS Compliance in 2025
To navigate the complex regulatory environment, businesses must adopt effective SDS management strategies.
1. Regular SDS Updates and Audits
- Conduct periodic SDS reviews to ensure compliance with OSHA, EPA, and state regulations.
- Update SDS whenever new hazard data, regulatory updates, or chemical composition changes occur.
2. Digital SDS Management Systems
- Implement cloud-based SDS management for easy access and retrieval.
- Ensure data encryption and secure storage to protect sensitive information.
3. Employee Training on SDS Usage
- Train employees on how to read, interpret, and follow SDS guidelines.
- Conduct hazard communication training to improve workplace safety.
4. Working with Compliance Experts
- Collaborate with regulatory consultants or SDS service providers to maintain compliance.
- Stay updated with government alerts on chemical regulations.
5. Proactive SDS Risk Management
- Monitor chemical exposure risks and update SDS accordingly.
- Ensure SDS information is accessible to first responders and health professionals.
- Maintain thorough records of all SDS updates for auditing purposes.
Conclusion
The impact of chemical regulations on SDS requirements continues to evolve, shaping how businesses manage and communicate hazardous chemical information. Compliance with OSHA, EPA, and state regulations ensures workplace safety, environmental protection, and regulatory adherence.
By staying informed about regulatory changes, leveraging digital SDS management, and following best practices, businesses can maintain compliance while prioritizing safety. As chemical regulations advance, companies must proactively adapt to new SDS requirements to avoid penalties and ensure a safer working environment. Utilizing professional SDS Services can streamline compliance efforts and improve safety management.