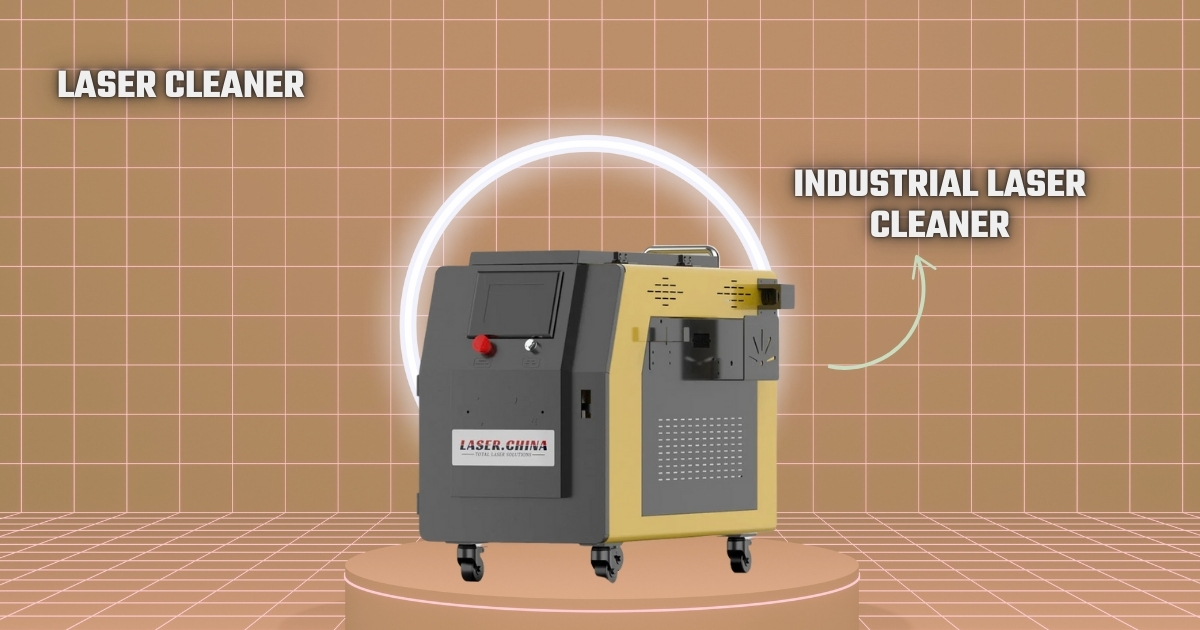
A fiber welder, also known as a fiber laser welder, is a high-precision welding machine that uses a focused fiber laser beam to fuse metal parts together. Unlike traditional welding methods like MIG, TIG, or arc welding, which use an electric arc or gas flame, a fiber welder uses laser technology to deliver heat with extreme accuracy. This modern solution is transforming industries such as automotive, aerospace, electronics, jewelry, and metal fabrication due to its speed, precision, and efficiency.
At the heart of a fiber welder is a fiber laser source—a type of solid-state laser that transmits energy through flexible fiber optic cables. This laser beam is highly concentrated, allowing it to melt metal surfaces quickly and form a strong, clean weld. Because of this focused energy, fiber welders create a narrow heat-affected zone, which helps reduce material distortion, cracking, or discoloration—common issues with traditional welding techniques.
One of the main advantages of a fiber welder is its unmatched precision. The laser can be directed to microscopic areas, making it ideal for small or intricate welds where accuracy is crucial. This capability is particularly useful in industries that work with tiny components or tight spaces, such as electronics, battery packs, sensors, or medical instruments. For example, fiber welders can join ultra-thin metal sheets or delicate parts without causing thermal damage to surrounding areas.
Another significant benefit is speed and efficiency. A fiber welder can complete welds up to 3–10 times faster than conventional methods, depending on the material and thickness. This faster processing translates to reduced labor costs, quicker turnaround times, and increased throughput—making it especially valuable for high-volume manufacturing environments.
Fiber welders are also favored for their clean and high-quality welds. The laser creates smooth, consistent seams that require little to no post-processing, such as grinding or polishing. The result is a visually appealing, strong weld that maintains the material’s structural integrity.
In terms of versatility, fiber welders can be used on a variety of metals, including stainless steel, carbon steel, aluminum, titanium, copper, and even dissimilar metals. Whether it’s a simple repair job or a complex custom fabrication, a fiber welder can adapt to the task. Many machines now offer features like handheld welding guns, auto wire feeding, and multi-mode settings (e.g., spot welding, seam welding, stitch welding), expanding their use across multiple applications.
However, the initial cost of a fiber welder is typically higher than traditional welding machines. That said, the investment often pays off due to the long-term benefits—reduced waste, less rework, lower energy consumption, and improved product quality.
In summary, a fiber welder is a powerful and efficient tool that is rapidly becoming the go-to solution for modern welding applications. With its precise control, clean results, and high-speed performance, it offers manufacturers and metalworkers a competitive edge in both quality and productivity.