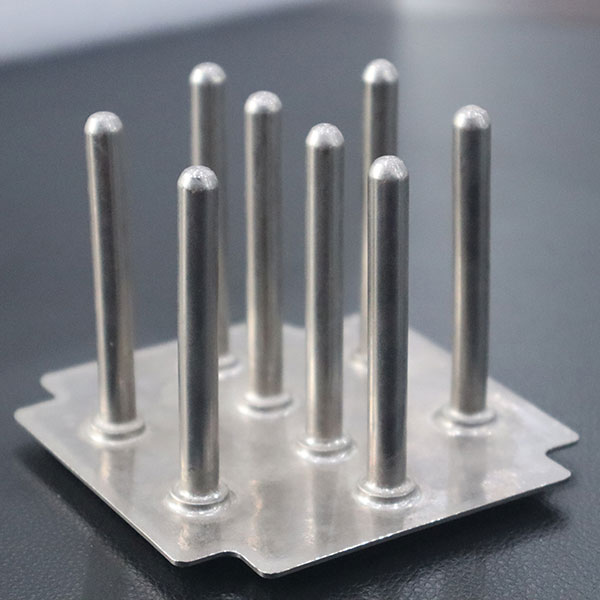
In the rapidly evolving world of science and technology, the ability to innovate is often directly linked to the tools and equipment available to researchers and developers. As industries push the boundaries of what’s possible, the need for more precise, efficient, and reliable systems becomes increasingly important. One of the most groundbreaking advancements in research and development (R&D) equipment is the 3D vacuum chamber—a device that is rapidly transforming various scientific fields, from material science and aerospace engineering to semiconductor manufacturing and biotechnology.
A 3D vacuum chamber is an advanced, three-dimensional system designed to create a controlled, low-pressure environment where researchers can conduct experiments or tests with minimal interference from external factors such as air pressure and humidity. The unique 3D structure of these chambers allows for more efficient usage of space and enhanced functionality, making them essential tools for modern R&D processes. Unlike traditional vacuum chambers, which rely on simple two-dimensional designs, the 3D vacuum chamber offers several key advantages that are revolutionizing the way scientific research is conducted.
What is a 3D Vacuum Chamber?
Before diving into how 3D vacuum chambers are revolutionizing R&D, it’s important to understand what they are and how they differ from traditional vacuum systems. A vacuum chamber is a sealed enclosure designed to create a vacuum—an environment where the pressure is significantly lower than the atmospheric pressure. This low-pressure environment is essential for conducting a wide variety of experiments, particularly those that require the removal of air or other gases to prevent contamination, oxidation, or chemical reactions.
A 3D vacuum chamber, as the name suggests, takes this concept a step further by incorporating a three-dimensional design that enhances the chamber’s ability to manage complex experiments. Traditional vacuum chambers are typically flat or cylindrical, which can limit the amount of space available for equipment or sample materials. However, 3D vacuum chambers use more intricate shapes and configurations, providing greater flexibility in design and functionality.
The addition of a third dimension allows for improved heat dissipation, better distribution of the vacuum, and a more efficient use of the chamber’s volume. This makes them ideal for experiments that require precision and consistency, such as those in fields like nanotechnology, electronics, and materials research.
How Do 3D Vacuum Chambers Work?
The core functionality of a 3D vacuum chamber revolves around its ability to create a controlled, low-pressure environment by removing air and gases. While the process of creating a vacuum is similar to that of traditional chambers, the 3D design brings several advantages to the table, especially in terms of space utilization and operational efficiency.
- Sealing and Evacuation: The 3D vacuum chamber is sealed tightly, typically made from durable materials like stainless steel or aluminum, to ensure that no external air can enter. Inside the chamber, a vacuum pump is used to evacuate the air, creating the desired low-pressure environment. The advanced 3D structure ensures that the vacuum is evenly distributed throughout the chamber, even in areas that might be difficult to reach in traditional designs.
- Precision Control: Once the chamber is evacuated, researchers can introduce various gases or other materials into the environment, allowing for precise control over the conditions within the chamber. This is particularly useful for experiments that require specific atmospheric conditions, such as chemical vapor deposition (CVD), ion implantation, or thin-film deposition.
- Enhanced Heat Management: One of the primary advantages of a 3D vacuum chamber is its ability to manage heat more efficiently. The increased surface area of the chamber allows for better thermal distribution, which is critical in experiments that involve high-temperature processes. The 3D design enables more effective heat transfer, reducing the risk of hotspots and ensuring that the chamber remains at the optimal temperature for sensitive experiments.
- Material and Sample Handling: In many R&D applications, it’s important to manipulate materials or samples within the chamber without introducing contaminants. The 3D vacuum chamber offers more space and flexibility for specialized equipment, such as robotic arms or sample holders, to perform these tasks without compromising the integrity of the vacuum.
The Advantages of 3D Vacuum Chambers in R&D
The use of 3D vacuum chambers in research and development offers several significant advantages over traditional two-dimensional vacuum chambers. These benefits include increased space efficiency, enhanced thermal management, improved sample handling, and more precise control over experimental conditions. Let’s analyze these benefits more closely:
1. Maximized Space Utilization
In many R&D labs and industrial settings, space is at a premium. Traditional vacuum chambers often require large, bulky systems that can take up considerable floor space. The 3D vacuum chamber, on the other hand, offers a more compact and efficient design, making it possible to conduct complex experiments in smaller, more confined areas. This makes it easier to integrate these chambers into research labs with limited space while still providing all the necessary functionality.
2. Superior Thermal Management
Effective thermal management is crucial in many R&D applications, particularly those involving high temperatures or rapid heating and cooling. The 3D vacuum chamber design enhances heat dissipation by increasing the surface area available for heat transfer. This allows for better control over the temperature within the chamber, ensuring that sensitive experiments can be conducted without the risk of thermal fluctuations that could impact the results.
3. Enhanced Flexibility and Customization
Every research project has unique requirements, and the ability to customize the design of a vacuum chamber can be a significant advantage. 3D vacuum chambers are highly customizable, allowing researchers to modify the internal layout, add specialized equipment, and adjust the chamber’s shape to accommodate specific experimental needs. This flexibility makes them suitable for a wide range of applications, from semiconductor fabrication to biomedical research.
4. Reduced Contamination Risk
In many research fields, even the smallest amount of contamination can compromise the integrity of the results. The 3D vacuum chamber is designed to maintain a highly controlled environment, minimizing the chances of external contaminants entering the chamber. Additionally, the advanced design allows for better sample handling and manipulation, reducing the need to open the chamber during experiments and further lowering the risk of contamination.
5. Increased Precision and Control
Many cutting-edge experiments require precise control over factors such as pressure, temperature, and gas composition. The design of 3D vacuum chambers makes it easier to monitor and control these variables with greater accuracy. Whether you’re conducting materials testing, testing new semiconductor components, or performing biological research, the ability to fine-tune the conditions inside the chamber ensures that you achieve more reliable and repeatable results.
Applications of 3D Vacuum Chambers in Research and Development
The unique capabilities of 3D vacuum chambers make them highly versatile and suitable for a wide variety of R&D applications. Some of the most notable uses include:
1. Semiconductor Manufacturing
In the semiconductor industry, precision and contamination control are of utmost importance. 3D vacuum chambers are widely used in processes such as thin-film deposition, ion implantation, and chemical vapor deposition (CVD). These chambers help ensure that the manufacturing process occurs in a low-pressure environment, preventing contamination and ensuring high-quality components.
2. Material Science and Nanotechnology
Material scientists and nanotechnologists rely on 3D vacuum chambers to create controlled environments for developing new materials and conducting experiments at the nanoscale. The ability to manipulate the chamber’s internal conditions allows for the synthesis of novel materials, including nanomaterials and composites, while maintaining precise control over the environment.
3. Biotechnology and Biomedical Research
In biotechnology, 3D vacuum chambers are used to create sterile, low-pressure environments for experiments involving biological samples, such as tissue cultures or protein synthesis. The ability to control temperature and humidity inside the chamber is critical for maintaining the viability of biological materials.
4. Aerospace and Space Exploration
Aerospace engineers use 3D vacuum chambers to simulate the harsh conditions of space and test spacecraft components under extreme low-pressure environments. These chambers help ensure that spacecraft and satellites are built to withstand the vacuum of space, which is critical for ensuring the safety and performance of these systems in orbit.
5. Energy Research
Researchers working on renewable energy technologies, such as solar cells and fuel cells, use 3D vacuum chambers to create controlled environments for testing and developing new energy solutions. These chambers help simulate real-world conditions, allowing researchers to test the efficiency and durability of energy components without external interference.
The advent of 3D vacuum chambers is revolutionizing research and development across multiple industries. With their superior space utilization, enhanced thermal management, and increased flexibility, these advanced chambers are enabling researchers to push the boundaries of innovation and achieve breakthroughs in fields ranging from semiconductor manufacturing to biotechnology.
At Tone Cooling Technology Co., Ltd., we are proud to be at the forefront of this technological revolution, providing cutting-edge solutions to support the research community in their quest for discovery. By leveraging the power of 3D vacuum chambers, you can ensure that your R&D processes are more efficient, precise, and effective than ever before. The future of research is here, and it’s powered by the innovation of 3D vacuum chambers.