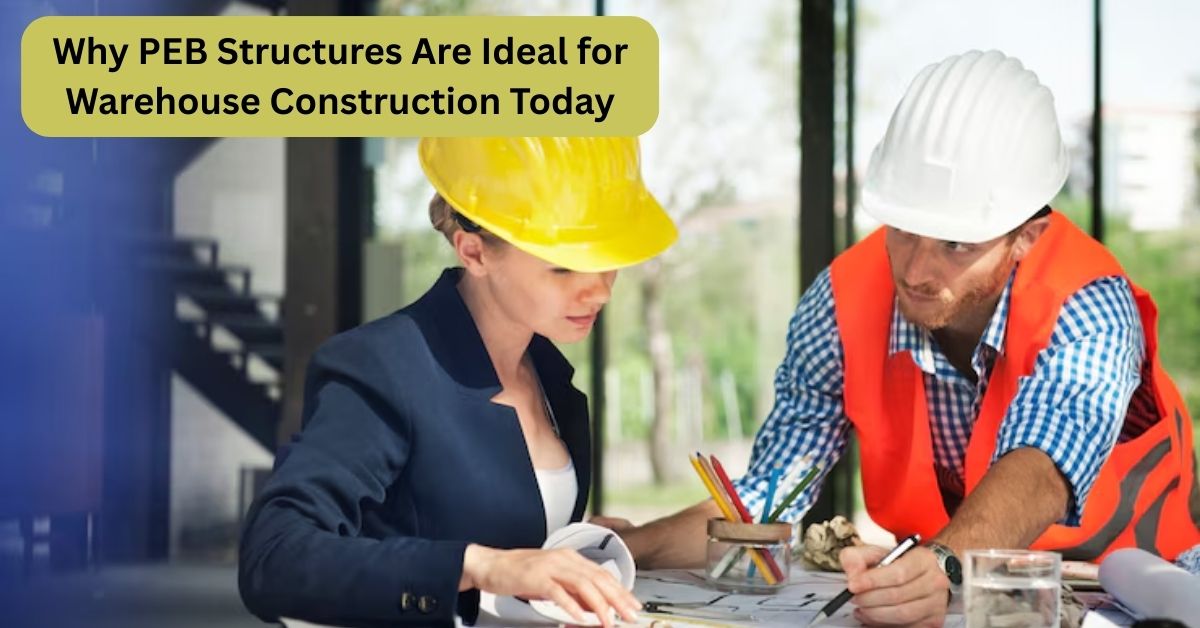
In today’s fast-evolving logistics and industrial sectors, the need for smarter, faster, and more sustainable construction has never been more critical. This is where Pre-Engineered Buildings (PEB) are making a significant impact especially in the warehousing segment. Across India, particularly in high-growth regions like Tamil Nadu, many Warehouse Construction Companies in Chennai are increasingly recommending PEB structures for warehouse projects due to their numerous advantages.
This modern construction approach is redefining how warehouses are built, providing speed, efficiency, and cost-effectiveness three vital elements for any growing business. In this article, we’ll explore why PEB structures are ideal for warehouse construction, the benefits they offer, and the role of today’s innovative Peb Construction Company in shaping this trend.
What Is a PEB Structure?
PEB, or Pre-Engineered Building, refers to a steel structure fabricated in a factory and then assembled on-site. These buildings are designed based on standardized dimensions and structural frameworks, allowing for quicker construction timelines and consistent quality. The components beams, columns, rafters, and wall panels are pre-manufactured and then bolted together at the construction site.
This concept significantly differs from conventional buildings, which involve cutting, welding, and fabricating each component on-site, a process that’s time-consuming and often labor-intensive.
The Growing Demand for PEB Warehouses
The logistics boom, driven by e-commerce, global supply chains, and smart storage needs, is fueling the demand for warehousing space in urban and semi-urban regions. Companies are no longer looking for just storage facilities; they need smart warehouses that support automation, high load-bearing capacity, and future scalability.
Enter PEB. These structures are proving to be the go-to solution for industries looking to expand rapidly and with reduced construction downtime. Many Warehouse Construction Companies in Chennai have recognized the economic and structural benefits of using PEBs in warehouse projects, thus making it a mainstream trend in industrial construction.
Key Advantages of PEB in Warehouse Construction
1. Faster Construction Time
Time is of the essence in warehouse development. Since PEB components are pre-fabricated, construction time is significantly reduced often by 30-50% compared to traditional methods. This allows businesses to become operational faster and reduce the cost of delays.
2. Cost-Effective Building Method
Budget constraints are a common issue in large-scale industrial projects. A Peb Construction Company can optimize material use through precise engineering, resulting in minimal wastage. Less labor, faster timelines, and controlled manufacturing costs make PEB a cost-effective solution.
3. High Durability and Low Maintenance
PEB warehouses are known for their strength and durability. The steel used in construction is resistant to pests, corrosion, and weather, which reduces maintenance requirements over the long term. Additionally, they offer excellent seismic and wind resistance when designed to local codes.
4. Design Flexibility and Customization
Modern warehouses often require custom layouts to support automation systems, specialized storage racks, or optimized workflow. PEB structures offer design flexibility, allowing builders to incorporate high ceilings, mezzanine floors, multiple docks, and more—all without compromising on structural integrity.
5. Environmentally Friendly
Sustainability is a significant concern in today’s construction world. PEB structures reduce environmental impact in several ways:
- Reduced construction waste
- Recyclable steel components
- Energy-efficient insulation options
- Smaller carbon footprint due to factory-controlled fabrication
This aligns with global trends favoring green buildings, making PEB a future-forward solution in warehousing.
Applications of PEB in Modern Warehouses
PEBs are not just used for basic storage structures. Their applications now cover:
- Distribution centers
- Cold storage facilities
- Fulfillment centers
- E-commerce warehouses
- Food and pharmaceutical storage units
- Automotive part storage
The adaptability of the PEB model allows Warehouse Construction Companies and other regions to cater to multiple industries with specialized needs.
How PEB Structures Enhance Warehouse Efficiency
Efficiency isn’t just about speed, it’s about smarter resource use, space management, and future scalability.
Space Optimization
PEBs can be constructed with large clear spans (up to 100 meters), allowing for obstruction-free internal space. This is crucial for smooth movement of forklifts, automated guided vehicles (AGVs), and large storage systems.
Energy Savings
With insulated panels and reflective roofing options, PEB warehouses can significantly reduce energy usage. This becomes particularly beneficial in regions with extreme temperatures.
Easy Expansion
Future growth can be accommodated with minimal disruption. Extensions or add-ons can be integrated seamlessly into existing structures, making scalability easier.
Why Chennai Is a Growing Hub for PEB Warehouses
Chennai’s strategic location as a manufacturing and logistics hub makes it an ideal location for industrial and warehousing developments. Ports, highways, and a growing logistics corridor have made it attractive for companies investing in distribution centers and storage units.
Many Warehouse Construction Companies are capitalizing on this opportunity by offering specialized services that focus on quick-to-erect PEB warehouse facilities.
In addition, policies from the Tamil Nadu government are encouraging industrial expansion through improved infrastructure, favorable regulations, and fast-track land approvals all of which align well with the PEB construction model.
Role of Peb Construction Companies in This Transformation
The execution of a successful PEB warehouse project depends heavily on the expertise of the construction company involved. A proficient Peb Construction Companies offers:
- Precise architectural and structural design
- Efficient project management
- Compliance with building codes and safety regulations
- Turnkey solutions from planning to final assembly
Their role extends beyond just fabrication; they act as a partner in end-to-end construction, ensuring that warehouses are built to last and function optimally.
The Future of PEB in Warehouse Infrastructure
Looking ahead, PEBs are set to become the backbone of industrial infrastructure in India. Advancements in technology such as Building Information Modeling (BIM), automation in manufacturing, and smart inventory systems are further accelerating the adoption of this construction style.
Some of the upcoming trends that will influence this space include:
- Smart warehouses with integrated IoT systems
- Use of AI for layout planning
- Modular warehouse units for plug-and-play scalability
- Use of 3D printing and robotic welding in PEB manufacturing
These innovations are strengthening the role of PEB as a sustainable and scalable warehouse solution across sectors.
Conclusion
PEB structures have emerged as a game-changing solution for modern warehouse construction. With their unmatched speed, durability, and cost-effectiveness, they offer the kind of operational agility today’s businesses need to stay competitive. In logistics-driven cities like Chennai, the rise of Warehouse Construction Companies that specialize in PEB structures is a strong indicator of the model’s growing relevance. For businesses planning to build efficient, scalable, and eco-friendly warehouses, partnering with a reliable PEB Construction Company is a strategic move aligned with current construction and industry trends. As industrial demands grow and sustainability becomes non-negotiable, the adoption of PEB in warehouse construction is not just an option, it’s the future.